Challenge
This Case Study is based on information provided by the AKT2I partners.
After water, concrete is the most widely used substance on Earth. If the cement industry were a country, it would be the third largest carbon dioxide emitter in the world with up to 2.8bn tonnes, surpassed only by China and the US*.
And yet, concrete is the material we rely on for so much of our modern development: our buildings, infrastructure, sea defences. However, as cement – the main ingredient in concrete – is responsible for 8% of carbon emissions**, there is an urgent need to find resilient, durable and low-carbon concrete solutions to help address the climate emergency.
As a leading UK supplier of precast concrete products, JP Concrete (JPC) is keen to innovate and research in this area, a desire which also reflects its clients’ requests for “green” concrete solutions that are also low-maintenance and durable.
To progress this innovation, JPC entered an AKT2I partnership with the University of East London (UEL) which has long-established material and structural laboratories and a wide range of advanced testing facilities. The teams were already in dialogue and the AKT2I support provided the right framework to formalise and accelerate their partnership and test innovative ideas.
Despite concrete being such a vital and widely used material, it cracks leading to corrosion of the steel bars reinforcing it. In the UK, repair and maintenance accounts for over 45% of the total expenditure on construction (the latter estimated at £120 billion annually***).
So the aim of this AKT2I was to find ways to improve the durability of low-carbon concrete products and examine key factors such as cracking, corrosion and early-age strength.
To this end, the partners aimed to develop an experimental study investigating the application of a pioneering, lower-carbon concrete mix that enables self-healing of cracks and protects steel bars, creating a more sustainable, resilient concrete solution.
New bio-agents were used for a novel mix of self-healing concrete to significantly extend the service life of infrastructure, especially that which is exposed to harsh environments, with applications for coastal defences, retaining walls, tunnels, culverts and below ground structures.
Outcome
A comprehensive laboratory testing programme was undertaken to examine the proposed novel concrete mix. This was focused on assessing the viability of adding two admixtures (one for automatic self-healing of cracks and the other for corrosion inhibition of steel bar reinforcement) and identifying the optimum mix.
The testing comprised measuring compressive and tensile strengths of the proposed low-carbon concrete product. Water permeability testing and photogrammetry were also undertaken to assess the crack healing. Accelerated corrosion tests were performed to assess the corrosion protection of steel bars embedded within the concrete.
Due to the availability of expertise and specialist testing facilities, the experimental testing of the new bio-concrete mixes took place at UEL which also provided space and IT equipment. A dedicated Associate was employed full-time on the project. JPC provided all materials and admixtures required and committed time from Innovation and Marketing Directors and Factory Managers. The close collaboration between academia and industry on this project allowed for the innovation to be realised.
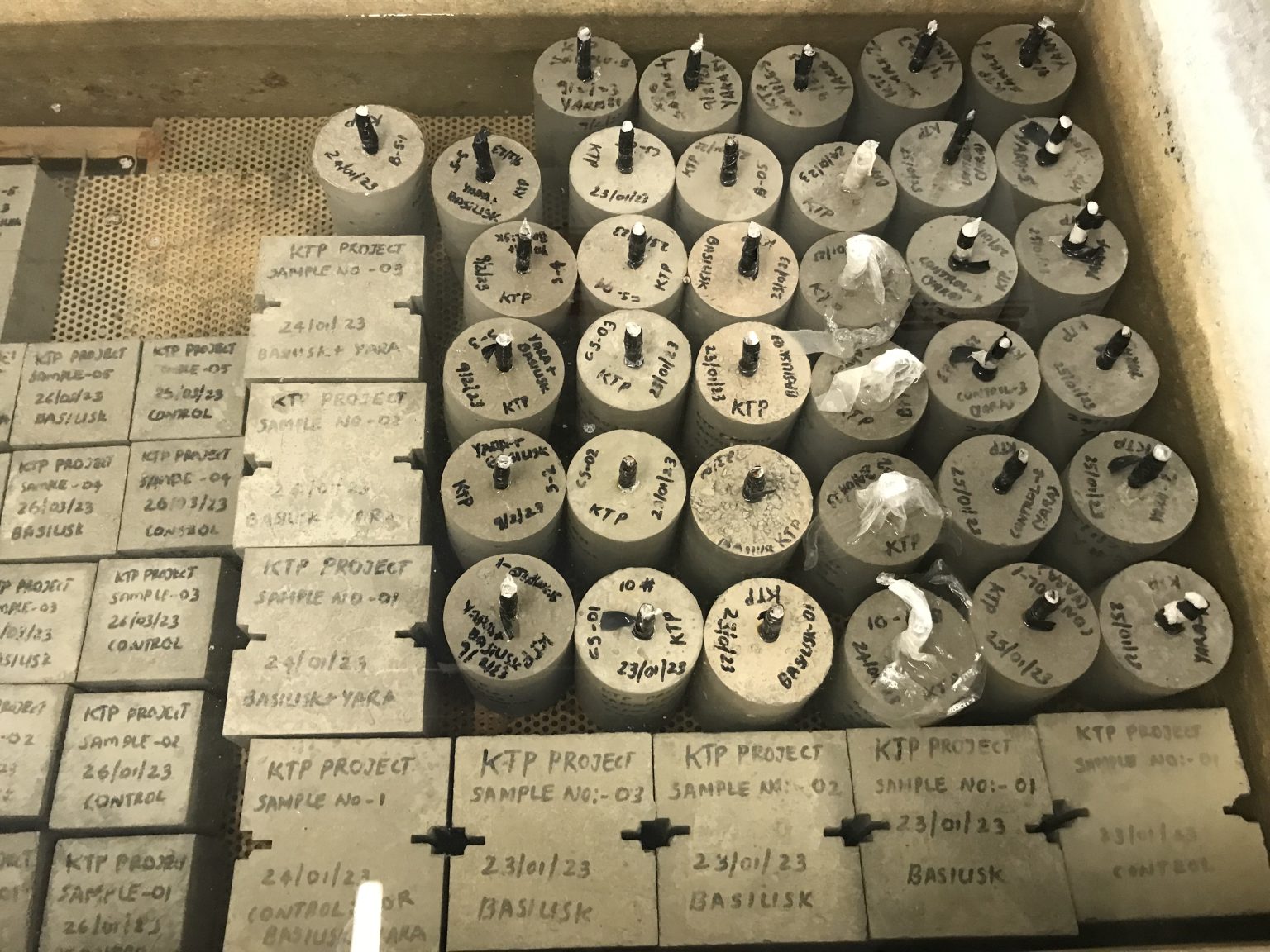
Impact
The AKT2I has helped accelerate the examination of certain concrete solutions and led to the development of a new lower carbon concrete mix which enables automatic self-healing of cracks in concrete (removing the need for manual repair and maintenance) and provides protection against corrosion (enhancing durability).
The project will enable longer life spans of low-carbon concrete solutions that will enhance ecosystem resilience, addressing societal challenges linked to Net-Zero Carbon. The AKT2I partners estimate that automatic healing of cracks and corrosion protection will save 15~20% of total maintenance costs, which translates to significant environmental and economical savings to the concrete sector as a whole (in the UK, repair and maintenance of non-housing construction accounts for around £64bn****).
The innovation will be applied to newly manufactured concrete products, especially sea defences and retaining walls. And the successful development of the new product range will also help scale-up current limited applications of sustainable structural walls for the next generation of “green” infrastructure networks, expanding JPC’s share of the low carbon concrete market.
Key benefits
The outcomes of this industry-academic partnership will lead to enhanced understanding of viable low-carbon innovative construction materials, with benefits for both parties – as well as the planet – and further collaboration between the partners is planned.
New testing methods were developed which will be useful in investigating future innovations in this challenging area; and UEL – which provided independent rigorous validation of new products, key in gaining the confidence of specifiers, contractors, and under-writers – has underlined its expertise in this sector.
As a result of the AKT2I, JPC (operating within the construction sector which is traditionally slow in responding to change and innovation) can now strategically position itself as an innovative force in the sector and the leading provider of self-healing concrete technology; and is able to make important strategic decisions about future new product development and marketing to clients and designers.
Without AK2I support, the partners confirmed that this innovation concept would not have progressed to the extent that it has.
What they say
“We are extremely pleased with the outcomes from the AKT2I research into corrosion inhibitors in concrete. Ali and the team have delivered another fantastic project and the findings will be extremely valuable in developing more resilient precast concrete products in the future.”
Further information
For more information about this project, contact Dr Ali Abbas, Associate Professor, University of East London: abbas@uel.ac.uk
* https://www.theguardian.com/cities/2019/feb/25/concrete-the-most-destructive-material-on-earth
***Construction statistics, Great Britain – Office for National Statistics
****Building Maintenance Costs and the Contribution to the UK Economy (bcis.co.uk)